Rekiseisha: A shining example of entrepreneurial spirit
From its samurai beginnings to the modern day, the story of Rekiseisha – producer of gilded hand-laid gold and metal leaf wall coverings that adorn luxury hotels and fashion houses – is an inspiring tale of resilience and innovation.
A few days after the atomic bombing of Hiroshima,10-year-old Hiroshi Hisanaga returned to the site of the 5-story wooden building that had housed the Rekiseisha gilded wallpaper factory and the family home. All that remained was a single storage unit, and a 27-meter-high chimney. He told a local newspaper in 2017 that he felt “an unutterable loneliness” as he looked at their home reduced to ashes. Rekiseisha’s rise from the ashes to supply wall coverings to some of the world’s biggest brands is a remarkable tale of resilience, but was not the first time that the family had had to overcome challenges created by forces beyond their control.
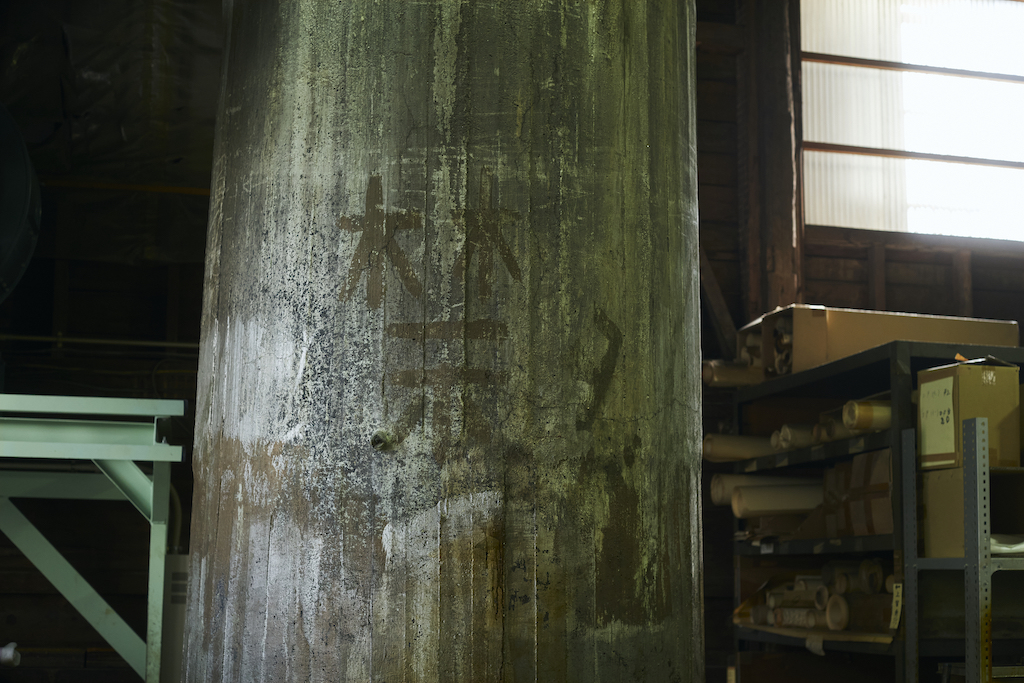
From samurai swords to interior design
In 1876, strict restrictions on the use of swords in Japan forced many of the nation’s swordsmiths to turn to manufacturing farm implements and knives. It was not only those that forged the swords that were affected, however, but those that had sold them too.
One such sword seller was Seijiro Hisanaga, the descendent of a merchant who had followed his lord to Hiroshima in 1619. Deprived of his main product, Seijiro switched to selling folding screens decorated with gold leaf paper which were a must-have item in the households of former samurai. It is to this astute pivot that the origins of Rekiseisha, which Seijiro would found in 1905, can be traced.
The gold paper used on the screens was made by applying gold leaf produced in Kanazawa to Japanese washi paper, and Kyoto, which used fine gold paper threads in kimono making, was, at the time, the center of gold paper production. Although there was money to be made in Hiroshima, there were long waits for shipments of Kyoto-made gold paper, and the entrepreneurial Seijiro started to consider making his own gold paper. Fortuitously, around this time, he was introduced to European brass leaf by a local picture frame maker.
All that glitters doesn’t have to be gold
As brass leaf has the appearance of gold and is cheaper to produce, it seemed like it could be an ideal replacement for gold leaf. However, as brass tends to discolor over time, making it inappropriate for celebratory occasions, he put his mind to inventing a processing method that would prevent discoloration.
After a decade of trial and error, Seijiro patented what would turn out to be Rekiseisha’s company’s golden (colored) goose – a new process by which brass leaf could be applied to paper in a way that it would retain its luster over time. It is a process that, although many have tried, over 100 years later, has yet to be replicated successfully.
Although Rekiseisha also continued (and still continues) to make real gold leaf paper, it was their brass leaf paper screens, renowned for a beautiful golden sheen that could be attained at a much lower price, that gained popularity throughout Japan. During the 1920s orders for gilded brass leaf wallpaper came from U.S. buyers and business continued to boom as its use in the domestic market as Japanese home design evolved.
War and recovery
“Fire is the test of gold; adversity, of strong men.”
Seneca
During World War II, the production of gilded decorations was considered a frivolous extravagance and Rekiseisha switched production to making paper for packaging military uniforms.
Seijiro lost two members of his family in the aftermath of the 1945 A-bombing and he himself was badly injured. Times were hard, but he gradually recovered and the company made ends meet by coating paper with coal-tar to provide waterproofing for the makeshift dwellings local people had put together after the bombing. Rekiseisha was eventually able to return to producing gilded paper, and, in 1959, rebuilt their factory around the surviving chimney and storehouse using materials from a nearby gymnasium and elementary school that had survived the A-bomb blast.
Post-war boom and artistic innovation
In an ironic twist of fate, when Japanese delegates went to the U.S. to research western hotel design as Japan prepared to welcome the world at the 1964 Tokyo Olympics asked about a certain kind of wallpaper that had caught their interest, they were surprised to be told that it was supplied by Rekiseisha back in Japan. It was a seal of approval that secured them a slice of the rapid development that Japan underwent in the coming years. They also benefited from an “oriental boom” in the U.S., which remains their most important overseas market. Today, the bulk of Rekiseisha’s business is wallpaper, split about 50/50 between overseas and domestic.
In addition to gold and brass leaf, Rekiseisha works with other metals, which include silver, copper, pewter, aluminum, and even platinum. Interesting colors and patterns are achieved through smoking silver leaf with sulfur to produce textured red, blue and black hues, a process that can only be performed by a highly skilled few.
Over a cup of coffee, liberally sprinkled with gold flakes, Ikuyo Fujii, Rekiseisha’s head of overseas development, explains that while metal leaf such as brass, and pewter may sound inferior to gold and silver, the lower cost of the raw materials allows for more investment in design, while maintaining an appearance over time that is indistinguishable from precious metals, thanks to Seijiro Hisanaga’s patented application method from the 1920s.
Having attracted the attention of some of the world’s top brands and, as well as adorning temples and shrines, Rekiseisha’s metal leaf paper can be seen in luxury hotels, restaurants and fashion houses, both at home and abroad.
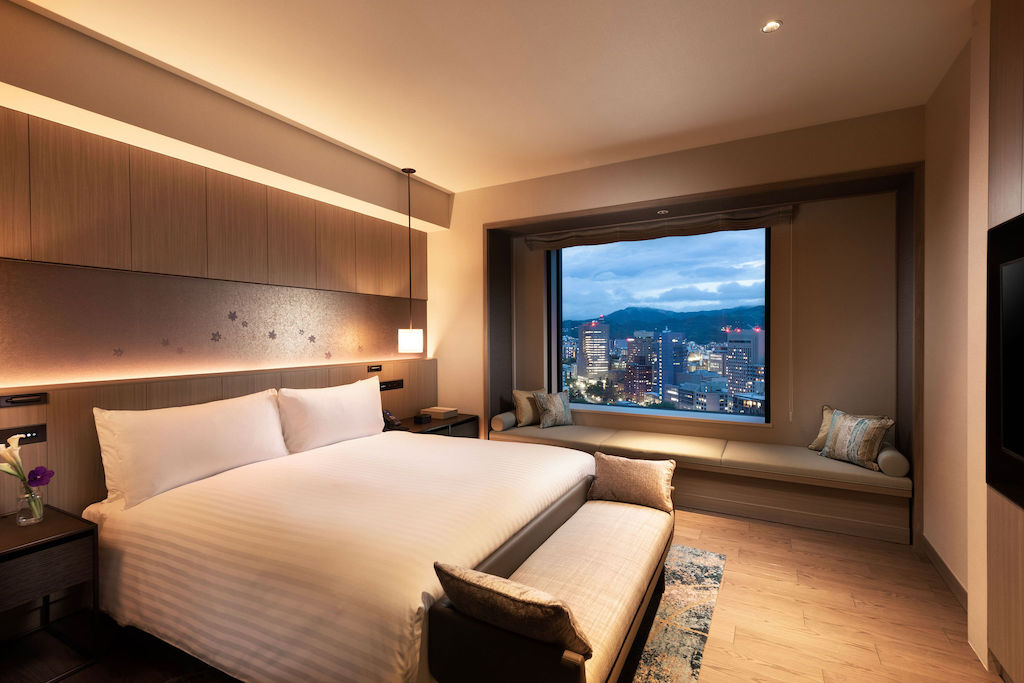
Rekiseisha’s versatility is on display at Hilton Hiroshima, where its metal leaf paper is used throughout. If you stay overnight, be sure to check out your headboard. Thanks to Rekiseisha’s application of brass leaf chips to blue organdy fabric, its appearance changes from blue to gold, depending on the angle from which you look at it. Yoshichika Ueda of Hirsch Bedner Associates, says that Rekiseisha allowed him to showcase traditional craftsmanship in a contemporary way.
On the day I visited the factory, Rekiseisha had just heard that they had won a contract to contribute to the interior design of a major fashion brand’s flagship store in the heart of New York City.
After congratulating Rekiseisha’s resident designers, Yuko Toishi and Chizuru Kubota, they tell me about the fine line that they need to tread between art and product design. They must capture the imagination of prospective clients, while ensuring that their ideas can be realized on the production line. Although excited by the prospect of working with metal leaf, both were new to the medium when they joined Rekiseisha, and spent several years working on the line to become acquainted with the material. Toishi says that despite this experience, the shift from idea prototype enabling the company’s craftspeople to replicate it consistently by the thousands is always a challenge.
“Real gold is not afraid of the melting pot.”—Chinese proverb
Despite Rekiseisha’s unmatched quality in its production of hand-laid metal leaf coverings, utilizing specially commissioned Japanese washi paper, in a world in which 99% of wallpaper is now vinyl, continued success is by no means secure. In the spirit of his predecessors, 6th generation president Tomoyuki Hisanaga is actively trying to think out of the box and pursue ways to increase awareness of the value of the work that they do and enhance Rekiseisha’s branding beyond the people within their own industry.
In addition to collaborative projects with artists and fashion designers, Rekiseisha has developed a range of lifestyle products that they hope will add a little glitter to our everyday lives. Toishi puts it well, “We’d like people to see another side of gold. It is often associated with opulence, but it doesn’t have to be ostentatious. It can be very warm and human.” Fujii adds that the main dias in the United National General Assembly are backed by gold, a symbolic link, she likes to think, with Hiroshima’s peace message.
At 88 years old, Hiroshi Hisanaga, who despaired at the sight of the ruined factory as a young boy, continues to act as a company advisor and to pass on the experience of what he, his family and the people of Hiroshima suffered in those dark days. Step through a door at the back of Rekiseisha’s modern showroom, and you find yourself in a factory that is little changed from 60 years ago. A maze of corridors and staircases, fashioned from those repurposed A-bombed buildings link workshops in which craftspeople continue to build on the legacy of Seijiro Hisanaga. Rekiseisha, represents both the tragedy of Hiroshima and its inspiring recovery, tracing a line from Hiroshima’s samurai past to the present day, and, we hope, onto a bright future.
Although the details of Rekiseisha’s processing methods are a closely guarded secret, the company offers fascinating tours of its factory as part of its hands-on workshops. It is an excellent opportunity to work on gold and metal leaf, see the craftspeople at work and feel the history of this remarkable company.
Rekiseisha [歴清社]
January, 2024
Photos: Shota Matono